Early gas leak detection (including methane and hydrogen) is crucial in terms of safety and savings. Ultrasonic microphones are a traditional approach for detecting gas leaks, often placed outside the valve or container being monitored. The drawbacks to this approach are two fold:
- If the microphone is in the air outside the monitored equipment, it is remote from the potential leak site which is typically acoustically noisy and forces a very careful design in the electronics to discriminate against false positives. It also potentially introduces a slight delay in detection time due to the low speed of sound in air.
- If the microphone is placed inside the pressure zone, close to the anticipated leak source (e.g. a valve) that forces the design to be tolerant of whatever pressure, temperature, and chemical environmental factors exist in the zone.
There is a better way: the use of contact piezo ultrasonic vibration sensors that detect ultrasonic surface vibrations in the containment structures that are induced by the escape of the pressurized gas from the leaks. It might seem counter-intuitive to ‘listen’ to a flute by touching a piezo sensor to the surface of the instrument, however a) the vibration is there and, b) piezo sensors are indeed sensitive enough to pick it up.
This results in the following advantages:
- Acoustic noise from air-borne sounds in the environment are reduced substantially, simplifying filtering requirement.
- Signature-to-noise ratio for leaks is increased.
- Sensors, not needing to pick up air vibrations, can be quite solid and hermetically sealed in stainless steel and bolted in place either inside the vessel or outside on piping.
- Propagation time from leak incidence to pickup is reduced because speed of sound travel in solid piping is normally quite a bit faster than in air.
There is one more significant advantage to this ‘direct contact’ approach:
The piezo sensor itself can be designed as a ceramic-metal composite with a 3D shape sculpted to essentially act as an acoustic filter and/or enhancer of the frequency band of interest, thus raising the signal-to-noise ratio for a specific leak signature to a very high level.
- How They Work
- Piezo Ultrasonic Sensors are Essential for Early Gas Leak Detection
- Advantages Over Traditional Sensors
- Understanding Piezoelectricity
- In Conclusion
How They Work
Using a piezo ultrasonic detector in tandem with signal processing electronics and novel software can help you determine with certainty where and when the leak occurs, as well as the severity of the leak. By precisely sensing the ultrasonic acoustic frequencies generated by the gas leaks and then processing the electrical signals captured by the following electronics circuitry, ultrasonic sensors accurately detects the leaks without false positives or false negatives.
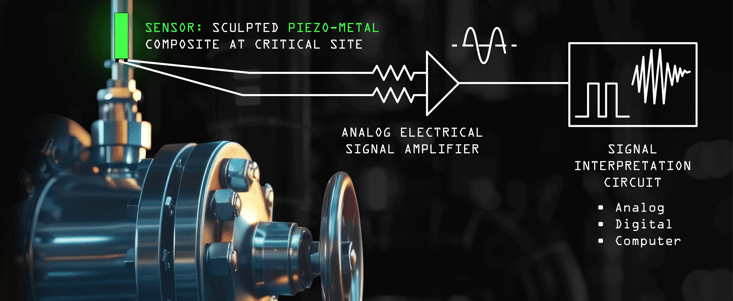
Piezo Ultrasonic Sensors Essential for Early Gas Leak Detection
Consider the common applications for piezoelectric ultrasonic sensors: motion sensing, flow detection, non-destructive testing, medical imaging, and many other industrial, commercial, and military applications. However, it is a popular sensing technology for gas leak detection, including hydrogen, methane, and carbon dioxide, as well as toxic gases. Whether transported via pipes or industrially stored containers, ultrasonic sensors are the right sensors for gas leak detection.
It’s not commonly known that gas leaks produce ultrasonic sound (like a whistle) but with frequencies above the audible range of 25 kHz. In addition, these leaks also produce vibrations in the physical structures, like pipes, containers, and other similar objects, which carry these gases. These ultrasound waves travel through both the air and the containing structures and even though they are quite faint, they can reliably be detected by piezoelectric ultrasonic sensors.
When given dedicated ‘on device’ mount (e.g. on a valve) compared to conventional gas leak detectors in the market, packaged piezo ultrasonic sensors offer a robust and reliable ability to rapidly – virtually instantly – detect such sound waves. What’s more, signal processing circuitry further interprets that sound or frequency to produce a defined signal. Simple microphones with threshold detection schemes cannot deliver this level of precision and accuracy.
Advantages of Using Piezo Ultrasonic Sensors for Early Leak Detection vs. Traditional Detectors
Piezoelectric ultrasonic leak detectors deliver many advantages over traditional infrared, catalytic, electrochemical, and other solid-state gas leak detectors, including:
- Precision and accuracy are demonstrated by the ability to instantly pick up (sense) ultrasonic signals generated by the sound of the gas leak from the walls of the pipe/container/valve.
- Broad capabilities regarding frequency range and the ability to be specific when detecting the signature of the leak. For example, detection of ultrasonic frequencies from 25 kHz to over 300 kHz or higher.
- Robust operations featuring a broader operational temperature range than traditional leak detection options – from cryogenic temperatures to high temperature environments such as within gas turbine engines.
- Cost savings by preventing losses due to fires, explosions, and other similar catastrophes.
- Real-time sensing from a remote location where human access is not practical.
Example of a piezo ultrasonic leak detector.
Understanding Piezoelectricity
It is a unique class of material which, when deformed by applied stress, produces a usable electric charge, and when subjected to an applied electric field, it can deform itself. In other words, a unique characteristic of the piezoelectric effect is that it is reversible. Such a unique characteristic enables the material to exhibit both the direct piezoelectric effect (the generation of electricity when stress is applied) as well as the converse piezoelectric effect (the generation of stress when an electric field is applied).
The converse piezoelectric effect is what makes power ultrasonic devices commercially feasible. While natural crystals exhibit piezoelectricity, quartz being a good example, artificial (homegrown) crystals also display much higher electromechanical conversion effectiveness and are exclusively used for the power ultrasonics. Lead zirconate titanate (PZT) compound-derived ceramics are primarily used for these devices.
But not all PZTs are good for this application. If not designed or protected well, PZT can be problematic. Because it is a ceramic, it can be brittle and present many failure issues, specifically when loaded in tension.
There are two developed technologies to substantially improve the robustness of bare PZT materials without compromising their reliability and performance. One involves bonding the PZT material to a metal shim with a very durable and high-strength bond. This technology provides a good amount of mechanical protection for the PZT.
However, the second technology involves fully encapsulating the PZT material using copper-clad and etched materials. This encapsulation, better known as “packaging,” protects the PZT both mechanically, as well as from the environment. Etching of the copper-clad materials also allows for full customization of the electronic circuit needed to robustly and reliably connect the PZT to its drive, sensing or harvesting electronics.
In Conclusion
Embracing piezoelectric ultrasonic sensors for gas leak detection marks a significant advancement over traditional methods. These sensors, with their ability to detect high-frequency ultrasonic sounds produced by gas leaks, offer a superior alternative in terms of precision, accuracy, and reliability. Their broad frequency range, robust operation in extreme temperatures, and cost-effectiveness due to prevention of hazardous incidents make them an invaluable tool in ensuring safety and efficiency.
Understanding the underlying principle of piezoelectricity, and how it's harnessed in these sensors, reveals the ingenuity of this technology. The use of Lead zirconate titanate (PZT) ceramics, especially when properly encapsulated and bonded, further enhances the durability and effectiveness of these sensors.
As an engineer, it’s exciting to see such technological advancements being applied to critical safety measures. Piezo ultrasonic sensors are not just about detecting leaks; they represent a leap towards smarter, safer, and more efficient industrial practices. Remember, when it comes to gas leak detection, it’s not just about responding to leaks, it’s about doing so with the utmost accuracy and reliability – and that's precisely what piezo ultrasonic sensors offer.
Power Ultrasonics Series
Part 1. Power Ultrasonics: Its History and the Technology
Part 2. Horn Transmission and its Applications
Part 3. Tonpilz Transmission and its Applications
For more information visit www.piezo.com.
Rob Carter
Principal Mechanical Engineer (Piezoelectrics) at Piezo.com